航空航天与力学学院李岩、杨伟东团队通过3D打印过程时变热场优化实现连续纤维增强复合材料增材制造缺陷有效控制,相关成果发表于《增材制造》
来源:航空航天与力学学院
时间:2023-09-04 浏览:
近日,我校航空航天与力学学院李岩教授、杨伟东研究员课题组提出了采用激光加热方式优化连续纤维增强复合材料3D打印过程中三维时变热场的策略,建立了连续纤维增强复合材料3D打印过程的温度-浸渍度-强度(“三度”)增材制造多尺度模型,揭示了3D打印过程中局部温度历史信息对复合材料轴向强度的影响规律,实现了3D打印连续纤维增强复合材料的轴向强度的提升,为减少复合材料增材制造结构的制造缺陷、提升其力学性能提供了有效方法。相关研究成果“Process-dependent Multiscale Modeling for 3D Printing of Continuous Fiber-reinforced Composites”在线发表于《增材制造》(Additive Manufacturing)。
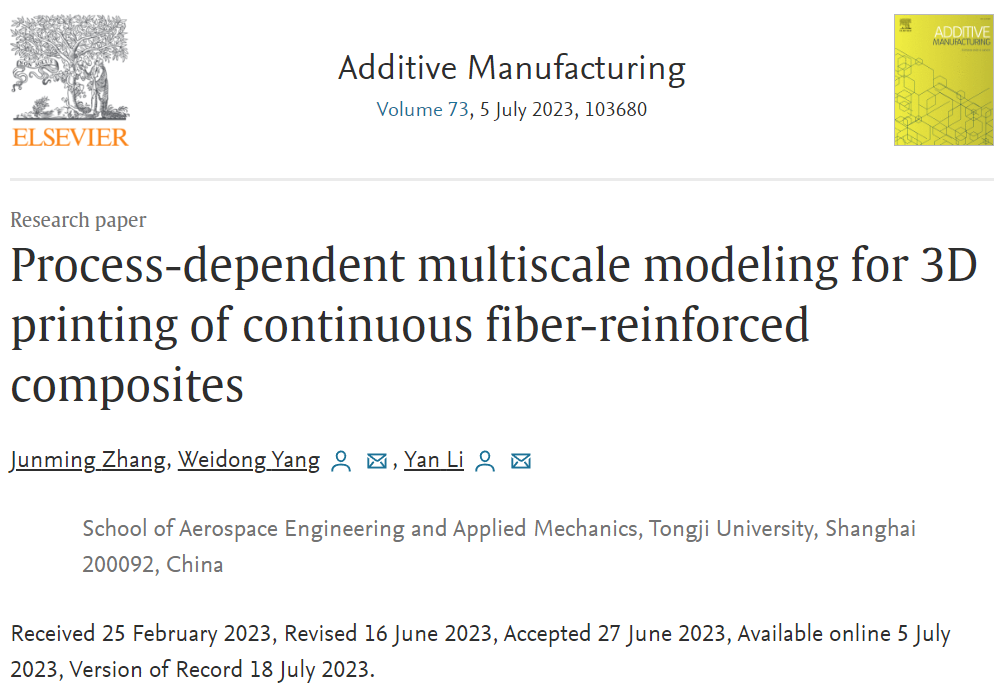
3D打印由于其高制造灵活性和高效率,在轻质复合结构领域具有广阔的应用前景。以3D打印为代表的增材制造技术,正在被广泛用于设计与制造各类几何形状复杂的多功能结构。然而,在连续纤维增强复合材料的增材制造过程中,由于多相材料只能在沉积位置附近获得短暂加热,并且高粘度的热塑性树脂在打印过程中的熔融时间极短,进而导致纤维束内的树脂浸渍不充分,最终使得3D打印的复合材料结构内部存在空隙缺陷。这些在3D打印过程中产生的初始缺陷是导致增材制造复合材料结构力学性能降低的主要原因,阻碍了3D打印连续纤维增强复合材料结构的工程应用。
基于3D打印的连续纤维增强复合材料零部件的各向异性特性可以丰富结构设计及优化方案,但其制造缺陷会导致力学性能显著降低。目前,针对连续纤维增强复合材料3D打印制造缺陷产生的机理研究仍然缺乏。该研究为了揭示连续纤维增强复合材料3D打印中的温度-浸渍度-强度定量关系,对3D打印过程中的三维热场和纤维束内受热驱动的树脂浸渍行为进行理论建模,并在模型中考虑了激光辅助加热的源项。基于浸渍程度仿真的结果,并考虑浸渍程度在空间中分布的不均匀性,该研究进一步建立了相应的增材制造力学多尺度模型,成功实现了复合材料增材制造结构轴向拉伸强度的预测。研究结果表明,通过在打印过程中施加外部热源,对增材制造时变热场进行改善,可有效提高3D打印连续纤维增强复合材料的轴向拉伸强度。该研究还对不同激光加热功率以及打印速度工况下的试样进行了实验与仿真结果的对比,二者的高度一致性证明了所提出模型的有效性。最后,该研究提出的理论模型准确描述了连续纤维增强复合材料在3D打印中的温度、浸渍度和拉伸强度之间的内在关系,构建了3D打印中工艺参数-细观结构-力学性能关系的控制优化方法,为高效增材制造高性能复合材料结构提供了理论基础,有望促进3D打印连续纤维增强复合材料在工程领域的广泛应用。
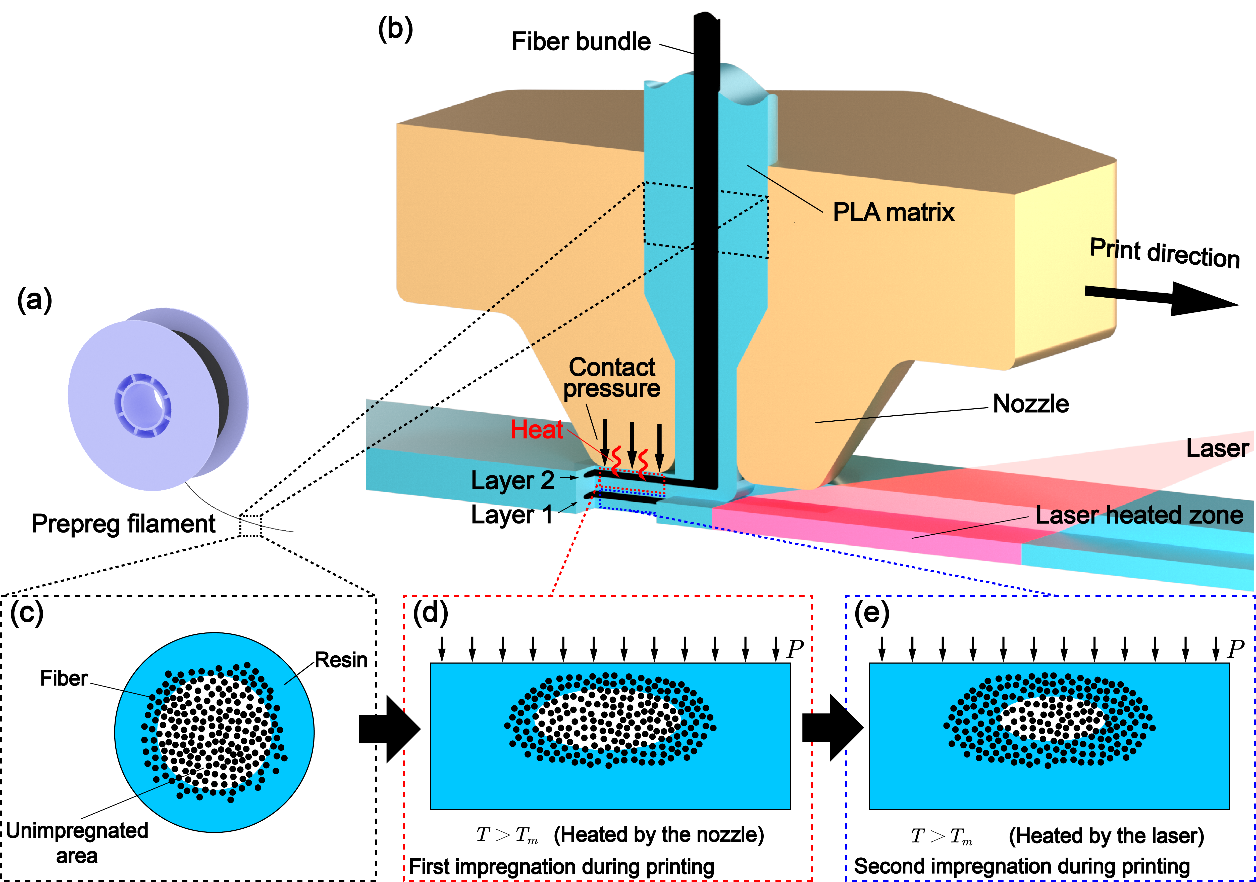
我校2020级直博生张峻铭为论文第一作者,李岩教授和杨伟东研究员为论文通讯作者。该研究工作得到了国家自然科学基金和上海高等学校特聘教授(东方学者)项目的资助。(杨伟东)
论文链接:https://doi.org/10.1016/j.addma.2023.103680